How carbide blades are made?
Carbide blades are valued for their exceptional hardness, wear resistance, and ability to maintain sharpness over extended periods, making them ideal for cutting tough materials.
Carbide blades are typically made using a process that involves sintering tungsten carbide powder into a solid form, followed by shaping and finishing the blade. Here’s a step-by-step overview of how carbide blades are generally produced:
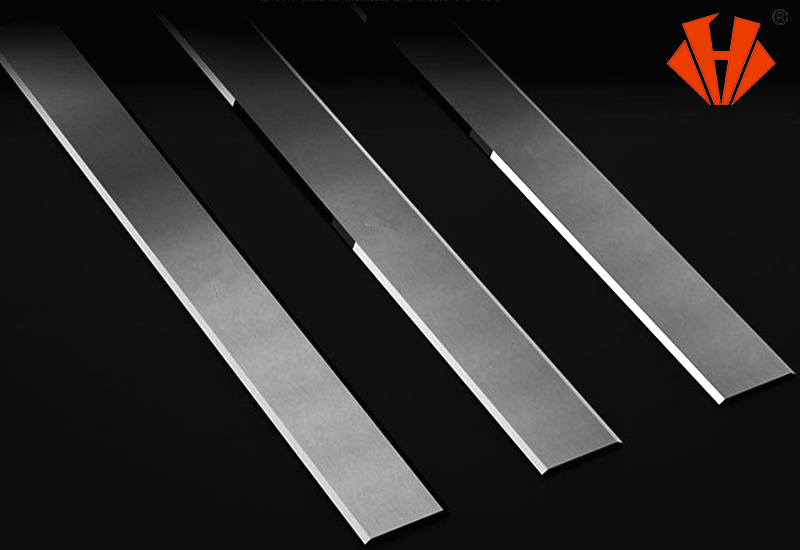
1. Raw Material Preparation
- Tungsten Carbide Powder: The primary material used in carbide blades is tungsten carbide (WC), which is a dense and hard compound of tungsten and carbon. The powder form of tungsten carbide is mixed with a binder metal, usually cobalt (Co), to help with the sintering process.
- Powder Mixing: The tungsten carbide powder and cobalt are blended together to form a uniform mixture. The mixture is carefully controlled to ensure the correct composition for the desired blade hardness and toughness.
2. Pressing
- Molding: The powder mixture is placed into a mold or die and pressed into a compact shape, which is the rough outline of the blade. This is typically done under high pressure in a process called cold isostatic pressing (CIP) or uniaxial pressing.
- Shaping: During pressing, the blade's rough shape is formed, but it is not yet fully dense or hard. The press helps compact the powder mixture into the desired geometry, such as the shape of a cutting tool or blade.
3. Sintering
- High-Temperature Sintering: After pressing, the blade undergoes a sintering process. This involves heating the pressed shape in a furnace at temperatures typically between 1,400°C and 1,600°C (2552°F to 2912°F), which causes the powder particles to fuse together and form a solid, dense material.
- Binder Removal: During sintering, the cobalt binder is also processed. It helps the tungsten carbide particles adhere to each other, but after sintering, it also helps to give the blade its final hardness and toughness.
- Cooling: After sintering, the blade is gradually cooled in a controlled environment to avoid cracking or distortion.
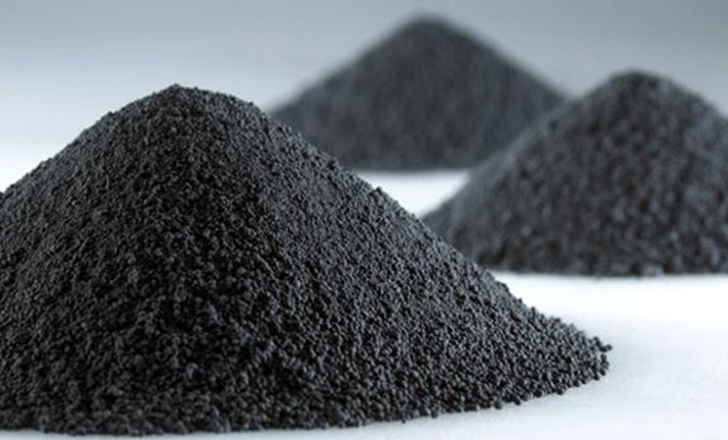
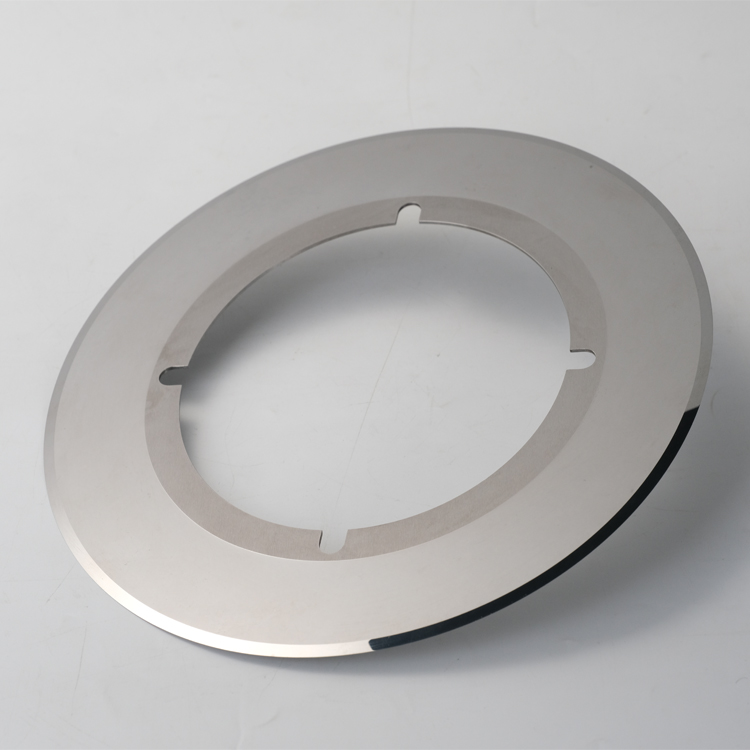
4. Grinding and Shaping
- Grinding: After sintering, the carbide blade is often too rough or irregular, so it’s ground to precise dimensions using specialized abrasive wheels or grinding machines. This step is essential for creating the sharp edge and ensuring the blade meets the required specifications.
- Shaping and Profiling: Depending on the application, the blade may undergo further shaping or profiling. This could involve grinding specific angles on the cutting edge, applying coatings, or fine-tuning the blade's overall geometry.
5. Finishing Treatments
- Surface Coatings (Optional): Some carbide blades receive additional treatments, such as coatings of materials like titanium nitride (TiN), to improve hardness, wear resistance, and reduce friction.
- Polishing: To further enhance performance, the blade may be polished to achieve a smooth, finished surface that reduces friction and improves cutting efficiency.
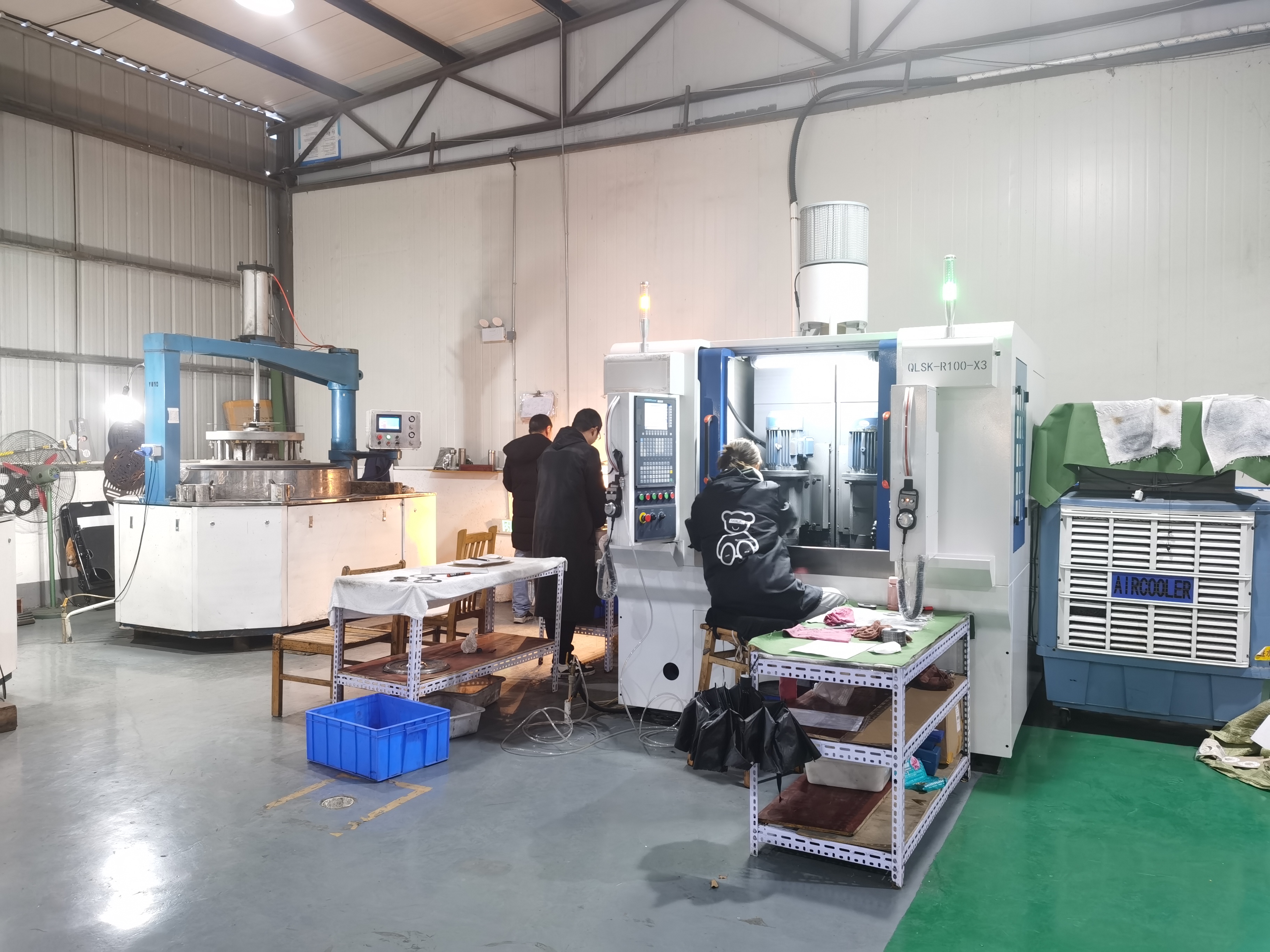
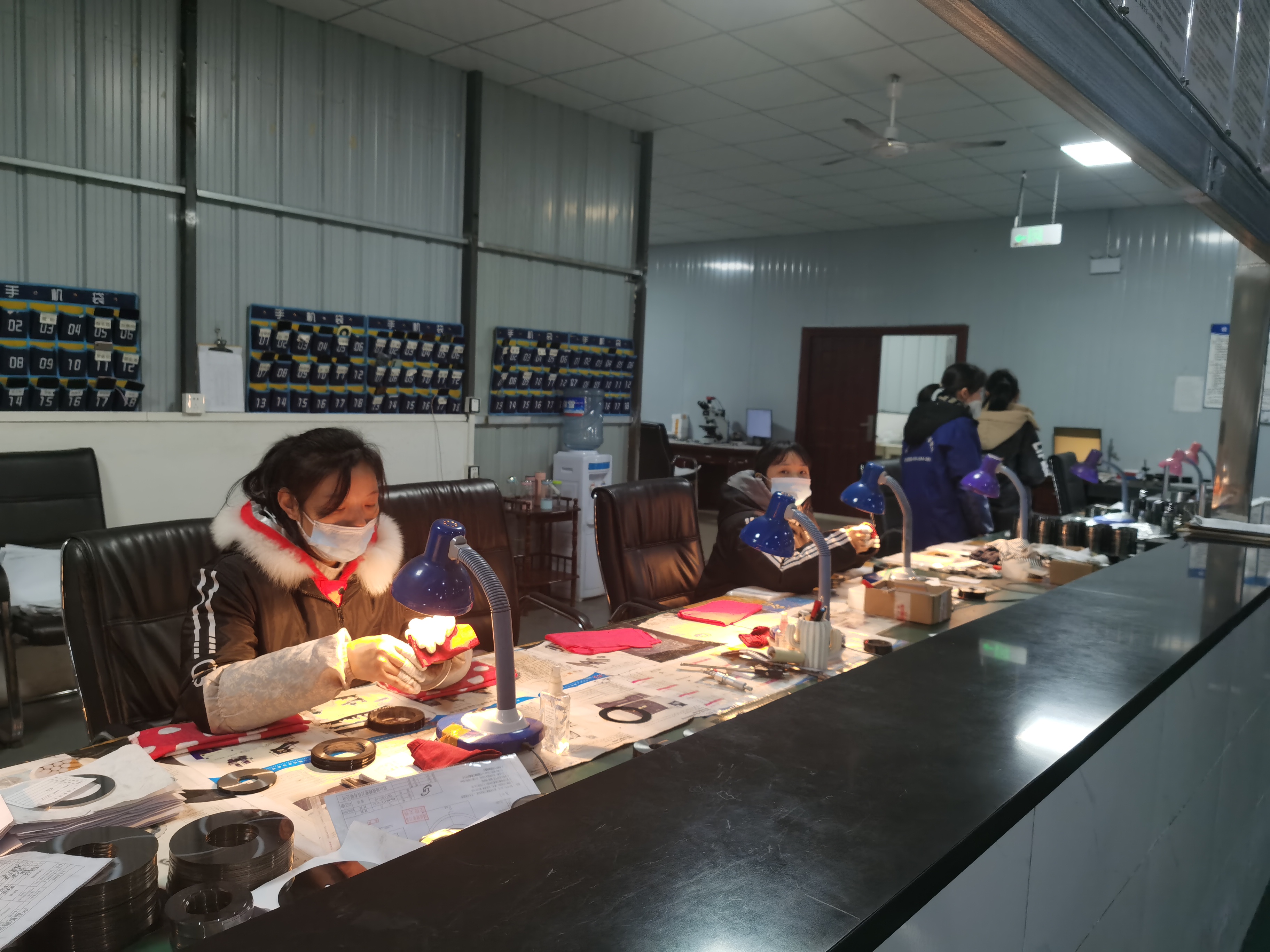
6. Quality Control and Testing
- Hardness Testing: The hardness of the blade is usually tested to ensure it meets the required specifications, with common tests including Rockwell or Vickers hardness testing.
- Dimensional Inspection: Precision is crucial, so the dimensions of the blade are checked to ensure they meet exact tolerances.
- Performance Testing: For specific applications, such as cutting or slitting, the blade may undergo real-world testing to ensure it performs as intended.
HUAXIN CEMENTED CARBIDE provides premium tungsten carbide knives and blades for our customers from different industries across the world.The blades can be configured to fit machines used in virtually any industrial application. Blade materials, edge length and profiles, treatments and coatings can be adapted for use with many industrial materials
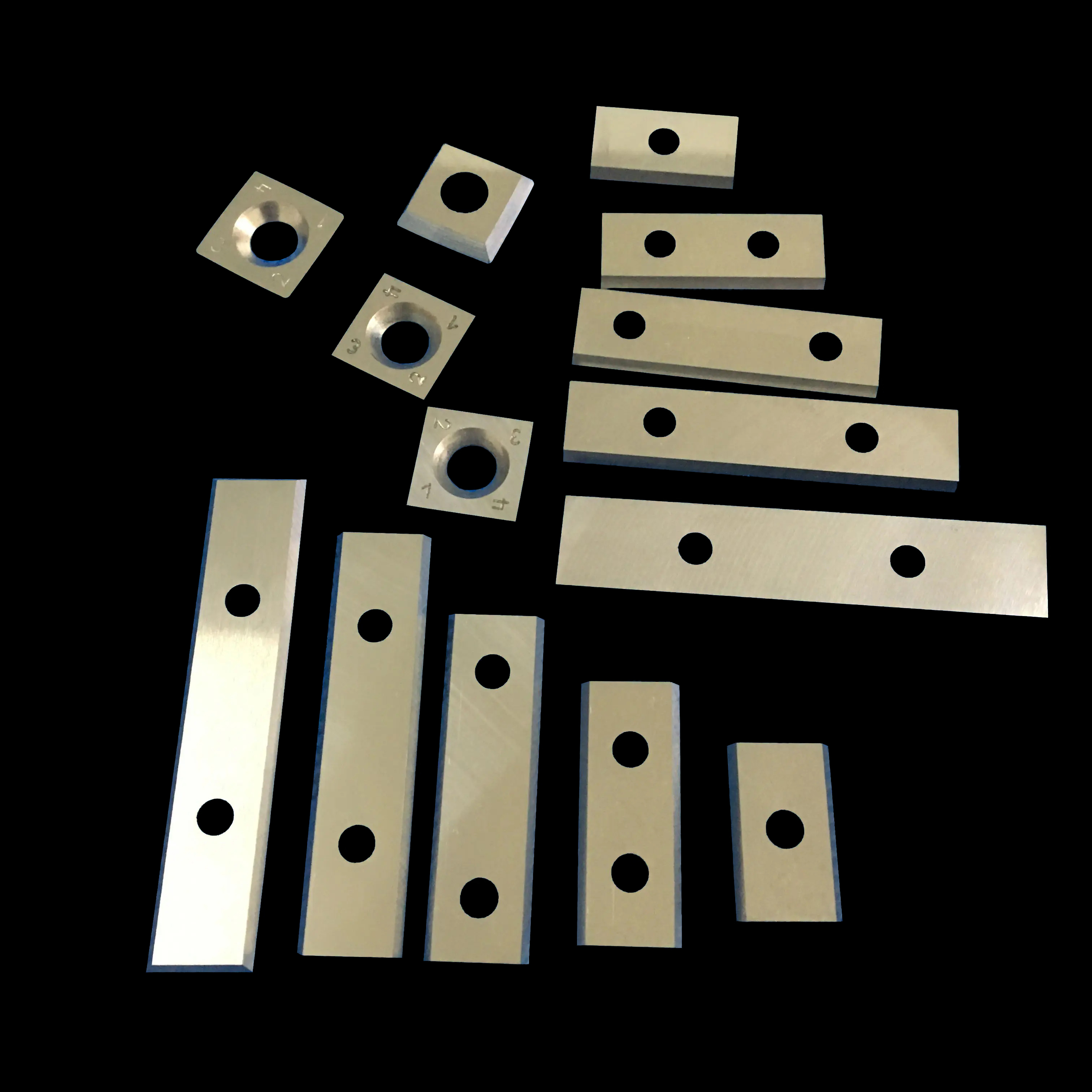
Once the blades have passed all quality checks, they are ready for use in various industrial applications, such as in metalworking, packaging, or other cutting operations where high wear resistance and sharpness are essential.
Post time: Nov-25-2024