Chemical Fiber Cutting Blades or Staple fiber cutter blade
Solid Tungsten Carbide (STC) and Solid Ceramic blades are both high-performance cutting tools, but they have distinct properties and applications due to differences in their materials. Here's a comparison of their applications based on key differences:
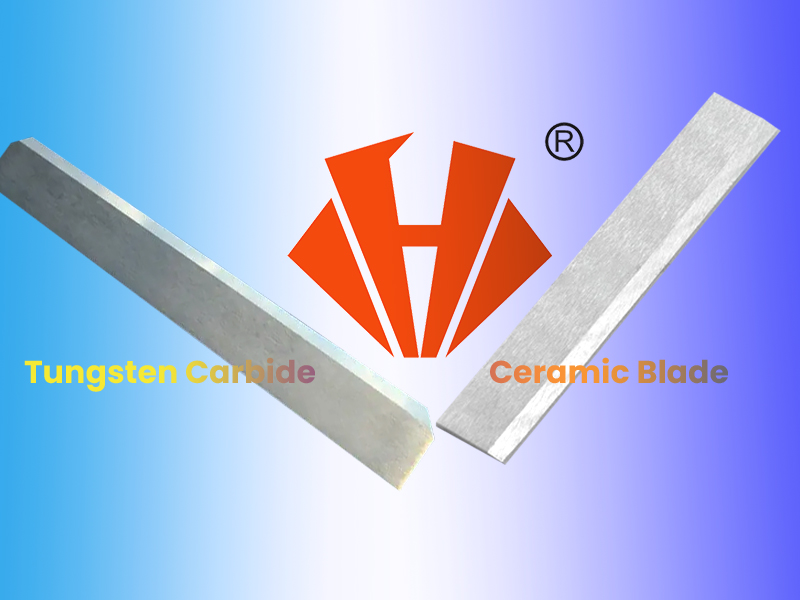
1. Material Composition and Properties
Solid Tungsten Carbide Blades
- Composition: Made from tungsten carbide, which is a combination of tungsten and carbon, often bonded with cobalt.
- Hardness: Extremely hard (close to diamond on the hardness scale), but less brittle than ceramics.
- Toughness: Offers excellent toughness, meaning it can handle impacts and high-pressure cutting better than ceramics.
- Wear Resistance: Very high wear resistance, suitable for long-term use in industrial settings.
Solid Ceramic Blades
- Composition: Typically made from materials like zirconia or silicon carbide.
- Hardness: Even harder than tungsten carbide, but much more brittle.
- Toughness: Low toughness compared to carbide, making it more prone to chipping or shattering under impact.
- Wear Resistance: Also highly wear-resistant but can wear unevenly when used on softer materials.
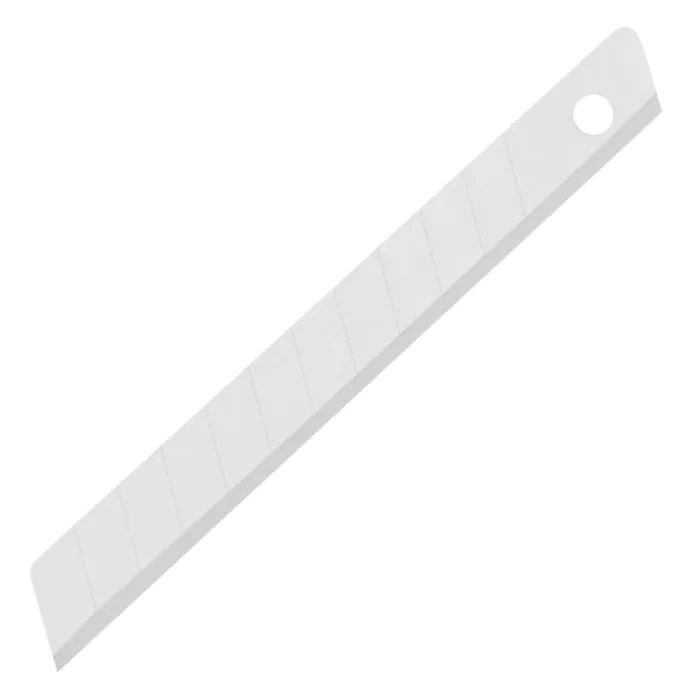
2. Applications
Solid Tungsten Carbide Blades:
- Metal and Composite Cutting: Preferred in heavy-duty applications such as cutting or machining metals, composites, and other hard materials.
- Precision Cutting: Used in applications requiring a balance between sharpness and durability, like industrial slitting (e.g., metal foils, films, and paper).
- High-Pressure Operations: Ideal for operations that involve high cutting pressure, such as drilling, grinding, and milling in industries like automotive, aerospace, and manufacturing.
- Longer Lifespan in Impact Conditions: Suitable for machinery where the blade may experience impact or vibration due to its toughness.
Solid Ceramic Blades:
- Precision Cutting of Softer Materials: Used in precision applications such as cutting film, fiber optics, plastics, and textiles. The extreme hardness provides exceptional sharpness but is usually reserved for less abrasive materials.
- High-Temperature Operations: Ideal in environments where high temperatures can affect cutting tools, as ceramics can maintain their properties in extreme heat.
- Corrosion Resistance: Often chosen in environments where chemical or moisture exposure could degrade metal blades, such as in food processing, medical applications, and the chemical industry.
- Delicate Applications: Used in situations where the material is delicate, and the blade must provide very fine, clean cuts (e.g., in electronics, semiconductor manufacturing).
3. Performance Considerations
Solid Tungsten Carbide Blades:
- Better suited for high-stress cutting applications due to its toughness.
- Can be resharpened multiple times, extending its lifespan.
- Higher tolerance for abrasive materials like metals and dense composites.
Solid Ceramic Blades:
- Ideal when the cutting environment requires minimal reactivity with the material being cut (e.g., medical blades).
- Not as tolerant to impact, so they are used in low-vibration, high-precision contexts.
- Typically, cannot be resharpened easily, making them more of a disposable option in some cases.
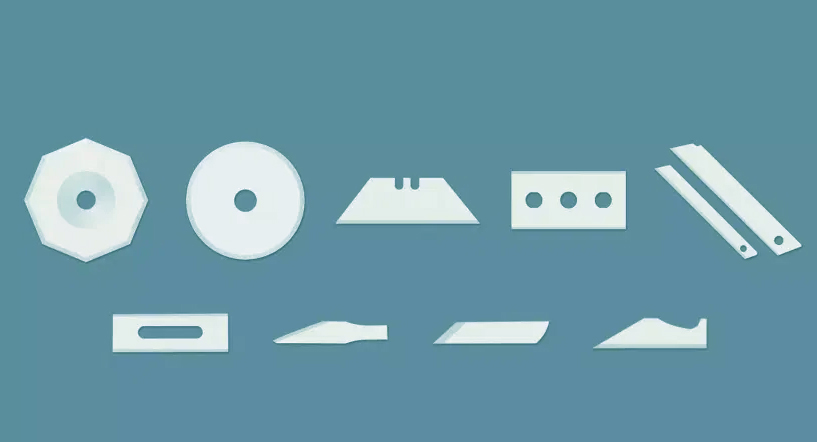
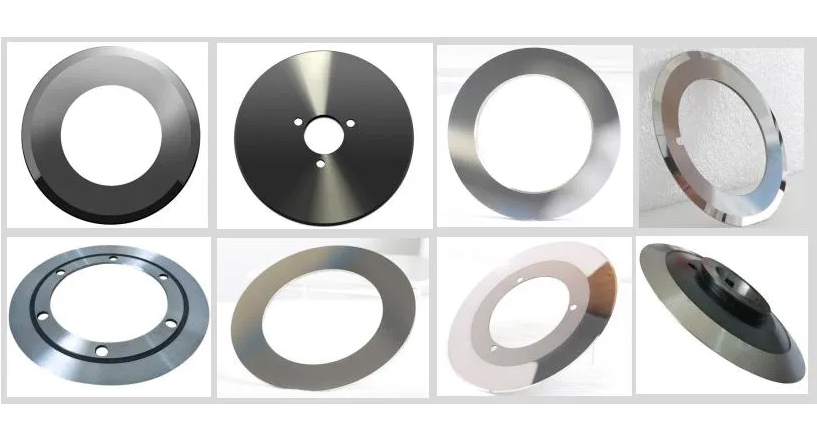
- Tungsten Carbide Blades are favored in industrial applications where toughness, durability, and wear resistance under pressure are key, particularly with harder or more abrasive materials.
- Ceramic Blades excel in precision, non-reactive, and high-temperature environments, cutting softer materials and in situations where chemical resistance is critical. They are not suited for high-impact or high-stress conditions due to their brittleness.
These differences guide the selection of each type of blade depending on the specific requirements of the cutting process.
HUAXIN CEMENTED CARBIDE provides premium tungsten carbide knives and blades for our customers from different industries across the world.The blades can be configured to fit machines used in virtually any industrial application. Blade materials, edge length and profiles, treatments and coatings can be adapted for use with many industrial materials
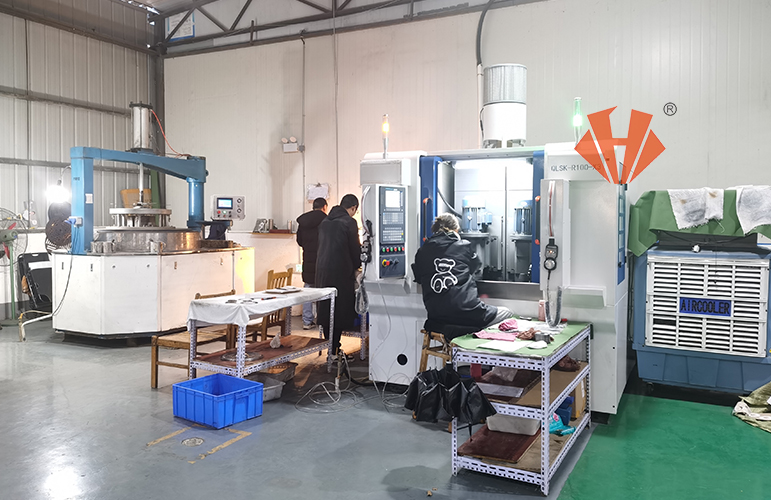
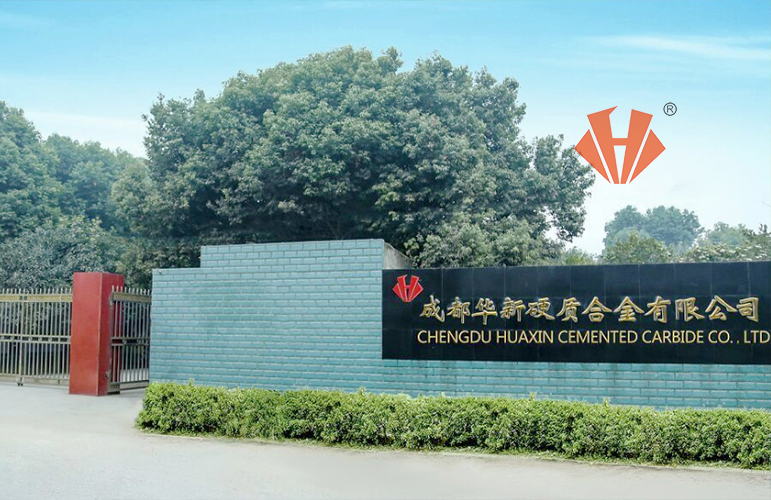
Post time: Oct-29-2024